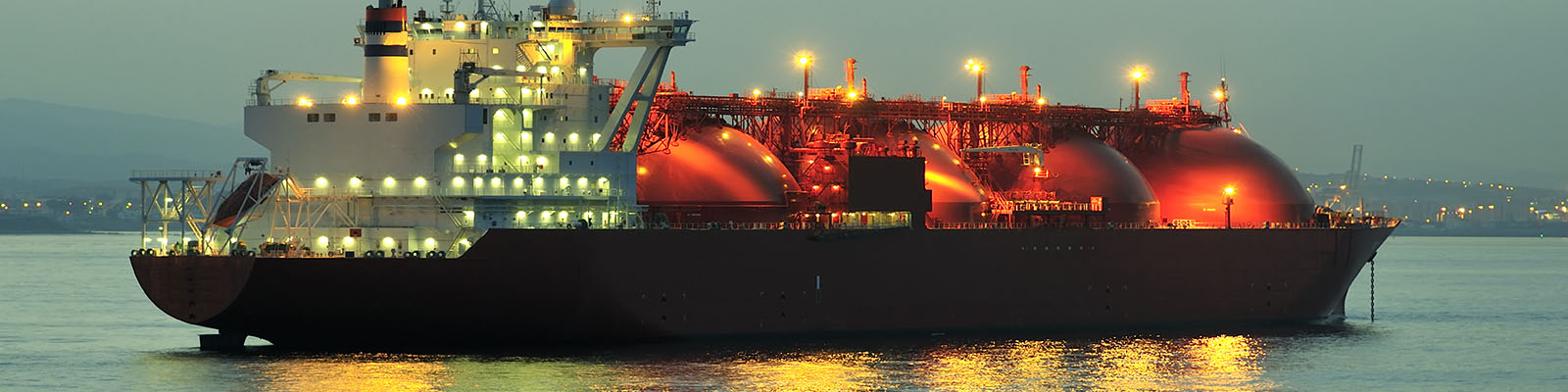
LNG Supply Chain
“Large Scale” LNG
Natural gas was experimentally liquefied for the first time in the 19th century. The first commercial transportation of LNG look place in the USA in 1941. Long distance LNG transportation started in 1959, between the USA and the UK. Regular commercial transportation started in 1964 between Algeria and the UK. Today there are more than 25 liquefaction plants and almost 100 regasification terminals worldwide.
Gas field: Natural Gas extraction and processing
After the raw Natural Gas is extracted, it is cleaned from impurities such as fluids and non-methane hydrocarbons during the purification process.
Liquefaction plant: Natural Gas liquefaction
During the liquefaction process, the Natural Gas is filtered to dispose of components such as dust, acid gases, helium, water and heavy hydrocarbons. It is cooled down further (cryogenic refrigeration) to approx. 163°C, at which point it liquefies.
Transportation by Sea
The volume of the liquefied gas is almost 600 times lower than the volume of the same quantity in gaseous form. This enables it to be economically transported over sea by specially designed LNG carriers. These are very well insulated to keep the LNG at the temperature of -163°C.
LNG Import Terminal – Regasification
LNG terminals like Revithoussa, serve two purposes: Keep the LNG in storage and compress and re-gasify it in order to supply a gas transmission pipeline. LNG can be distributed on a small scale from liquefaction and regasification terminals.
Small Scale LNG
In the last few decades, new uses of LNG have emerged, implying the LNG leaving the terminal in liquid form and not as gas: As marine fuel, as road transportation fuel and sea or road transportation of LNG to industrial or other clients
These new uses constitute the “small scale LNG” sector, where the LNG leaves the Import Terminal (i.e. Revithoussa) either in small LNG carriers or in road trucks.
Bunkering Methods
For sea transport, specially designed bunker vessels are used. LNG can be transported over land by tanker trucks or railway tankers.
Truck to Ship (TTS): Used over a decade. Typical ISO tank with 40 m3 volume is sufficient for the needs of a ferry operating between well defined, fixed routes. Bunkering rates: between 100m3/h. Strict safety procedures ensure minimised methane release during normal bunkering operations.
Ship-to-Ship (STS): Maybe performed alongside quays, at anchorage or at near-shore installations. It offers high degree of flexibility. Flow rate in a typical bunkering operation 1,000m3/hr.
Pipeline-to-ship (PTS): The least developed method. Mini-terminals (jetties) allow bunkering facilities.

The sole responsibility for the content of this webpage lies with the authors. It does not represent the opinion of the European Communities. The European Commission is not responsible for any use that may be made of the information contained therein.
Website Privacy Policy